- OTHM Level 5 Unit H/650/1142 Professional Supervision Assignment: Health & Social Care Case for Managing Supervision and Performance
- ATHE Level 4 Unit 15 Software Testing Frameworks Assignment: TDD and BDD Strategy for Medical Data Validation Script in Python
- ATHE Level 4 Unit 12 Web Design and Programming Assignment: CTO Birdwatching App Development for Urban Wildlife Insights
- ATHE Level 4 Unit 21 Synoptic Computing Project Assignment: Smart Parking App Design for Urban Mobility Solution
- ATHE Level 4 Unit 1 IT Systems Development Assignment: The World of Art Case Study for Global Online Sales Expansion
- CYP6032 Leading Multi-Agency Health & Social Care Assignment: Vulnerable Groups Literature Review and Reflective Evaluation
- Unit 21 – L/618/8101 Geotechnical Design Assignment 1: Scunthorpe Station Overpass & Bridge Infrastructure Proposal
- Y/616/7445 Unit 039 Diabetes Awareness Assignment: Understanding, Managing and Supporting Individuals with Diabetes
- DHCS 12 (M/650/5189) Understand Mental Ill Health Assignment: Explore DSM/ICD Disorders, Discrimination & Capacity
- Unit 8 Social Media Strategy Assignment 2: Planning, Execution & Evaluation for Organisational Growth
- CIPD Level 7CO01 Strategic People Management Assignment: Demographic Trends, Legal Reforms, Innovation & Resilience in the Workplace
- Financial Accounting Assignment: Lee’s Sole Trader Transactions & Cash Flow Analysis
- L/508/4603 NCFE Level 3 Sport and Exercise Massage Assignment 3: Consultation & Technique Review for Two Contrasting Athletes
- F/650/1141 Unit 4 Team Management and Recruitment Assignment: Health & Social Care Case Study for Effective Leadership and PDPA-Compliant Hiring
- R/650/1138 OTHM Level 5 Assignment: Working in Partnership in Health and Social Care
- NVQ Level 3 Health and Safety Risk Management Assignment: Practical Assessment and Workplace Application
- MBA7068 Strategic Portfolio Assignment 1: Global Business Trends and Managerial Skill Development
- Mechanical Services Innovation: Hotel Rotation Case Study for Energy-Efficient Heat Pump Integration
- K/618/4170 ATHE Level 3 Unit 4 Assignment: Working in Health and Social Care
- T/618/4169 ATHE Level 3 Unit 3 Assignment: Human Growth and Development in Health and Social Care
B51EM: You will be designing the “steel jacket” part of an offshore wind turbine (typically 3MW) of the type shown in Figure 1: Advanced Mechanics of Materials 1 Assignment, HWU, UK
University | Heriot-Watt University (HWU) |
Subject | B51EM: Advanced Mechanics of Materials 1 |
Part 1 – Design of structure
You will be designing the “steel jacket” part of an offshore wind turbine (typically 3MW) of the type shown in Figure 1. You will be “recycling” the design procedures for such structures, developed in the 1980s for offshore oil and gas production, Figure
1.1 Sizing of tubes.
Choose a frame configuration from the 3 options in Figure 3. Select key dimensions of tower and jacket heights and sketch jacket in 2D (example representation in Figure 4, showing reactions and loads). Consider wind loading on the rotor only and use the following for the thrust force on the rotor
where ρ is the air density, A the swept area, CT, the coefficient of thrust and v the wind speed. Convert Fw into a couple plus horizontal load (blue arrows in Figure 3) and decide on what reaction types you wish to use (orange arrows in Figure 3).
Ensure that your structure is statically determinate (number of members + number of reactions = 2 × number of joints). Analyse the jacket as a 2D pin-jointed frame (truss), using your estimated values of loads (weight of tower plus turbine, green arrow and rotor wind load, blue arrows). Note that this method assumes no moments at joints (or at loading or reaction points) and, hence, that each member is either a strut (in compression) or a tie (in tension).
Classify each joint as Y, K or X, and identify chord (member carrying largest load) and brace(s). Estimate the chord wall thickness, T, from:
where P is the axial force in the brace (in N), Fy is the yield strength of your chosen material (in MPa) and β is the diameter ratio, d/D. Then, obtain wall thicknesses and diameters for each member ensuring that their cross-section remains below yield in either tension or compression (Figure 5).
Finally, identify the location and magnitude of the “hot-spot” stress range, S, as a function of wind speed, v, Figure 6. The hot-spots are in the welded intersections between the members and are the areas most prone to fatigue
1.2 Fatigue life
Using spectral fatigue analysis, determine the fatigue life at the “hot-spot” using the method published by Williams and Rinne4 . First, find a wind loading spectrum for your chosen location, and then fit the closest Rayleigh spectrum that you can. Devise a relationship of the form 𝑆 = 𝑎𝑣 𝑏using your design considerations.
1.3 Discussion
Discuss your results critically. This means that you should assess the likely effect of the assumptions that you have made, including those you have been directed to make. You should also say what additional analysis (or measurements) you would need to do to improve your confidence in the design or, if inadequate, how you would improve the design
Part 2 – Design of rotor hub
Figure 7 shows a typical large wind turbine rotor hub design, made from a cast alloy (which you are free to choose). Simplify the design so that it is a cylindrical ring and calculate a suitable wall thickness, based on the circumferential stress at your highest anticipated rotational speed. You should assume that the ring is only subject to inertial loading so that it can be treated as a rotating disc (plane stress).
2.1 Defect assessment
Use the R6 procedure to determine the largest tolerable casting defects oriented in the radial and circumferential directions, respectively.
2.2 Discussion
Comment on your results and decide on appropriate inspection procedures at
installation and in service
Use the simple cantilever model of a turbine blade in Figure 8 and assume it to be a rectangular sheet made from an isotropic material.
3.1 Displacement functions
Choose appropriate values for the elastic moduli E and ν and calculate the profile of zdisplacement as a function of y (Figure 8) up to a value of δmax at y = L. Now, introduce a twist into the blade by assuming that the z-displacement at y = L is larger than δmax at x = 0 and smaller than δmax at x = B. Finally, write down equations for the displacement functions
3.2 Distribution of strain tensor
Using your answer to 3.1, and the small strain – displacement equations in Cartesian co-ordinates, determine the components of the strain tensor in the x-y plane. The components should be expressed as functions of x and y in microstrain, thus:
3.3 Map of maximum direct strain
Using your answer to 3.2, select four points in the x-y plane and find the magnitude and direction of the maximum principal magnification factor, M1. Show these in a map of the x-y plane as vectors.
3.4 Discussion
Comment on your results, including their relevance to a realistic composite turbine blade.
Buy Answer of This Assessment & Raise Your Grades
if you are an engineering student and need engineering assignment helper service to complete your B51EM: Advanced Mechanics of Materials 1 assignment within the deadline then connect with the expert writers of Students Assignment Help UK. you can also hire management assignment help and accounting assignment help at a reasonable price.
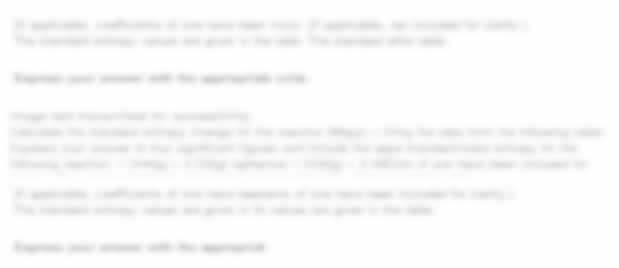